Films for TRACTION applications
Our high-quality capacitor films for traction applications are developed and produced with special attention to long lifetimes and demanding circumstances.
With our expertise, know-how and continuous R&D, we produce the highest quality capacitor films in the market – to answer to the needs of tomorrow.
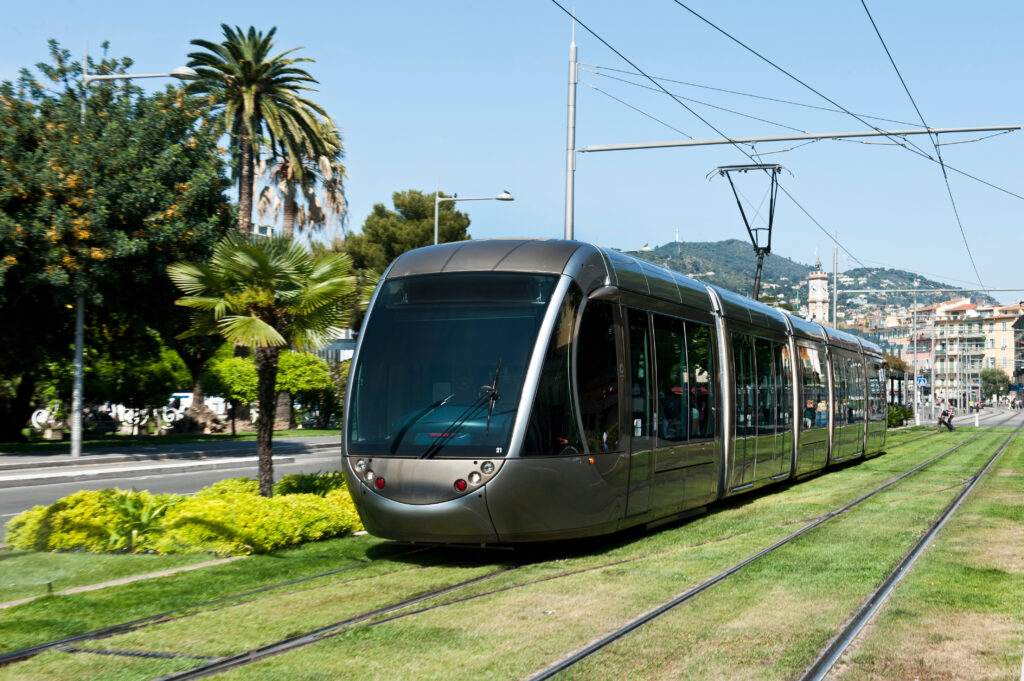
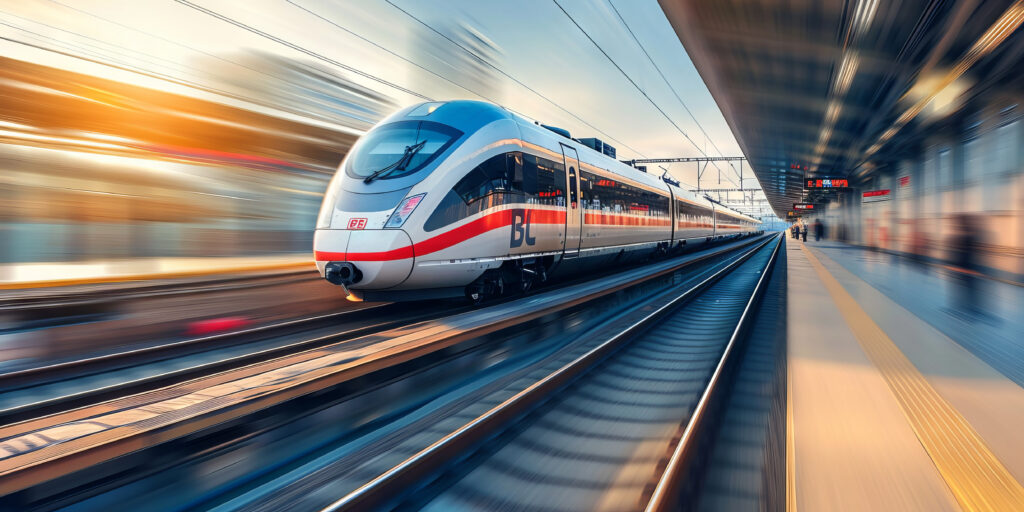
Modern high-speed trains and urban transport networks depend on energy-efficient electric traction motors. Our sophisticated metallised film solutions designed for traction control and locomotive capacitor applications withstand high electric and thermal stress levels.
Tervakoski Films Group is the only capacitor film manufacturer that includes the whole production chain in-house. This gives our customers the benefit of tailormade solutions, our own product development to enhance performance and reliable deliveries from a stable partner.
Superior quality through continuous R&D
100 years of expertise
Extensive know-how and expertise in production and R&D
Exclusive usage of our own
base film
Full product traceability is assured for every manufacturing step
Fully tailored products
Total production chain control enables tailormade solutions and guarantees product quality
Base film for metallisation
The base film for metallisation is PP impregnated film manufactured through the tenter process using super clean electrical grade high-temperature resin. This is a low shrinkage film with a controlled smooth surface on both sides and corona treatment on one side.
Our new generation of films (RERCT, ECTS) are designed for high ambient temperatures to meet the needs of high dielectric strengths and long durability in AC/DC applications. Available in thickness range starting at 6.0 um.
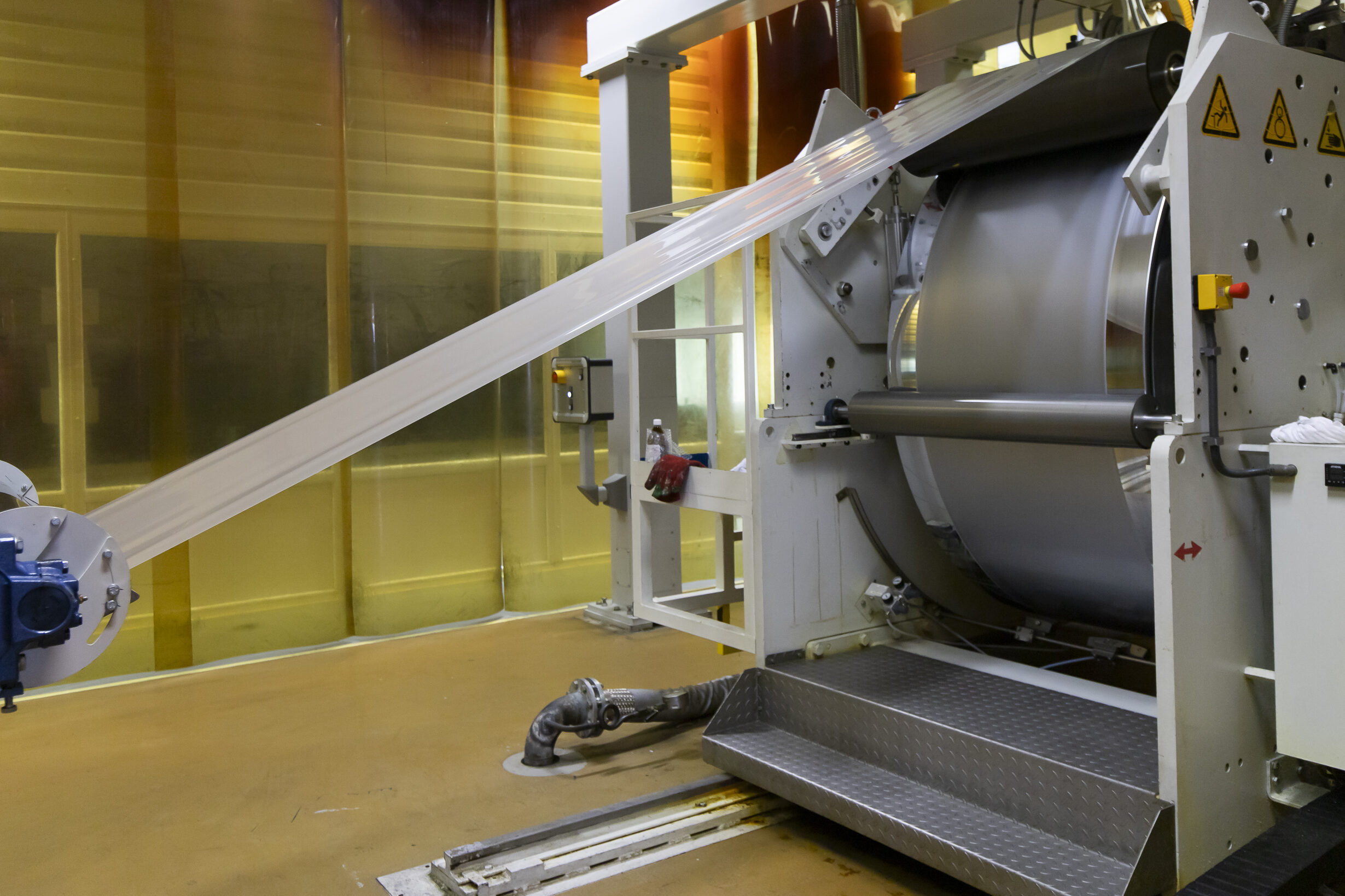
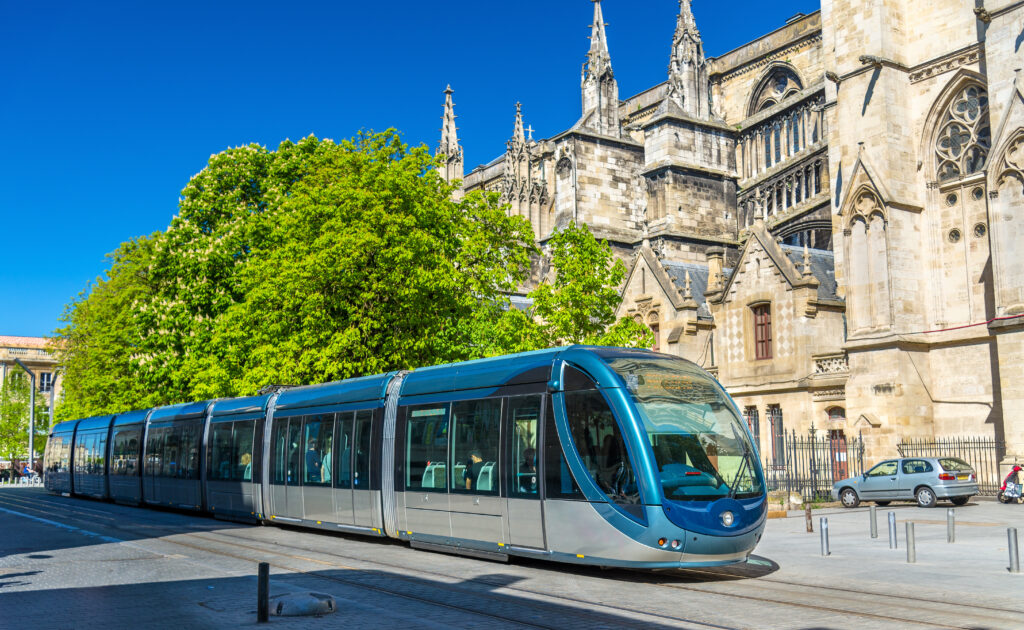
Metallised film for impregnation
Metallised film for impregnation in traction applications is dedicated to DC capacitor applications at high ambient temperatures. The film also displays excellent ripple current behaviour.
In order to guarantee film quality we only use our own hazy films in production (thickness range starting at 6 um). Metallising is done using a zinc-aluminium alloy or Bi-metal configuration (aluminium active area and zinc contact). All films are also available with a straight and/or wave cut margin. Depending on customer design (simple or internal series configuration) the resistivity profile can be either standard or individual.