Uncompromised quality and durability throughout the entire supply chain are key factors at Tervakoski Film.
Using sophisticated technologies, such as pattern printing on metallised film, we can ensure that our capacitors remain safe and efficient in both existing and future applications for decades.
The mission of capacitor film is to enable a capacitor to do its main job, which is to temporarily store electrical energy in an electrical field. For this to happen, two electrical conductors need to be separated by a dielectric material with next to zero electrical conductivity, thus providing the capacitor with the ability to store and return electrical energy. But what happens if the dielectric material, in this case an extremely thin polypropylene film, should break?
– With a controlled manufacturing process and high-quality materials, we can minimise the risk of breakage. However, since 100 per cent reliability does not exist, our metallised capacitor films have been developed to also handle minor defects. Our films have several safety mechanisms which allow a capacitor to keep running with only a minimal reduction in performance properties should any weak spots occur, explains Vladimír Monček, R&D Director at Tervakoski Films Group.
Self-healing property
Let’s first have a look at the basic safety mechanism; the self-healing behaviour (see infographic 1). This is the film’s ability to remove short-circuit conditions. Weak spots in the polypropylene film, caused for example by nonuniformities in the film structure, can potentially cause a short-circuit arc between the films at a certain voltage level. The heat generated by the arc makes both the metal layer and the films around the point of failure melt, thus stopping the process as the electrical contact is lost. The capacitor can keep running, even though capacitance equal to the area without metal is lost. Too extensive self-healing, however, gradually decreases capacitor performance properties and can eventually lead to total capacitor failure.
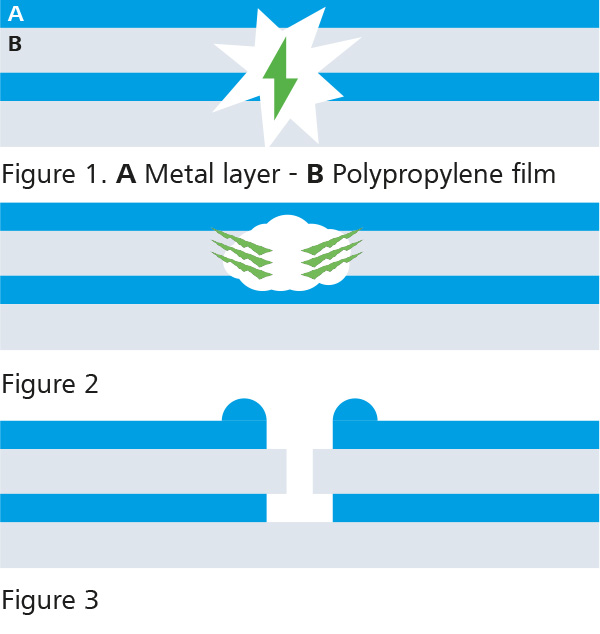
Infographic 1: Self-healing behaviour
The heat generated by the arc during a breakdown makes the plastic film and metal layers around the point of failure melt.
- Weak spot in polypropylene film (dielectric) through which an electric current will find its way at a certain voltage
level. This causes a shortcut between the films/electrodes with an electric arc. - Heat caused by the arc makes both the polypropylene film and the metal layer melt.
- The process stops. As the metal layers surrounding the hole have evaporated, the electric contact is lost. A total capacitor failure is prevented as short circuits cannot occur between the metal layers.
Controlled fault isolation using patterns
Tervakoski Film’s metallised film has excellent self-healing properties, but in certain applications, such as electric vehicles or Smart Grids, an additional safety feature called pattern metallisation is utilised to make the safe self-healing process more predictable.
In pattern metallisation, the film is divided into segments with patterns printed during the metallisation process (see infographic 2). The segments are connected to each other merely by micro fuses. During a short circuit, the high current burns out the fuses around the fault, efficiently disconnecting and isolating the affected area in a strictly controlled manner.
This reduces internal damage to the capacitor, which allows it to remain in service with only a minimal reduction in capacitance. One segment is typically no more than one square centimetre in size, a fraction of the total of 400-500 metres of film a single capacitor can easily house.
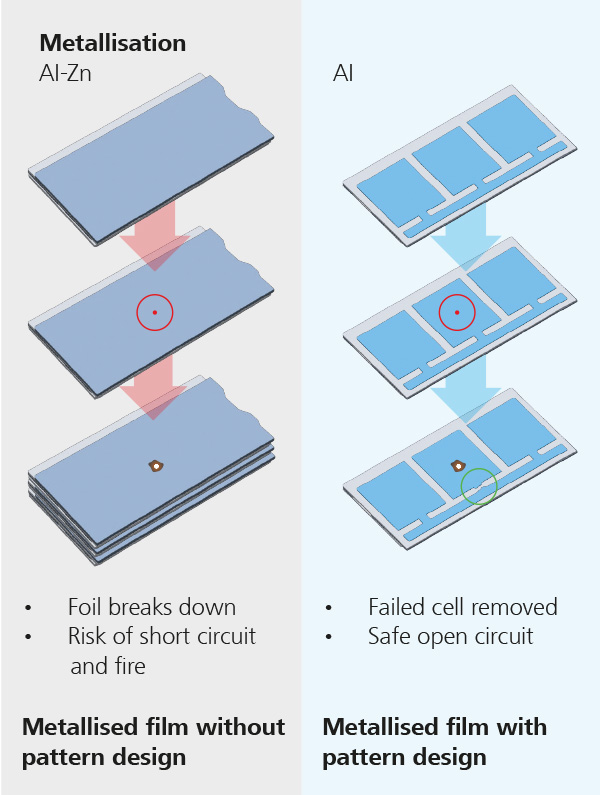
Infographic 2: Self-healing vs Patterns
Complex for a reason
As for the pattern design, Tervakoski Films Group follows the requirements and wishes of its customers to give the film the complex behaviour needed for the intended application of the capacitor.
– Different customers and apps require different things. For example, in applications such as electric vehicles and Smart Grids, the safety requirements and lifetime expectancy of capacitors are set exceptionally high. That is why our films also have different properties.
By adjusting the process parameters, we can achieve precise dimensions and ensure that the final film quality meets our customers’ expectations and high-quality standards, says Peter Hvizda, metallised film production manager at Tervakoski Film.
Printing patterns on metallised film is a complex procedure, requiring proper tool design and rigorous process control.
The pattern is printed during the metallisation process by a spatial sleeve fitted with the pattern lines and fuses. Special oil is applied to parts of the pattern sleeve surface before the pattern is then transferred into the film surface, thus preventing the evaporated metal from sticking to the film in those areas. Capacitance in the pattern lines is lost, but the increased safety makes it worth it.
The process also involves a free-margin tool that leaves the film’s edges empty, hence the name free margin. The free margin works as an electrical insulation to prevent shortcuts between two film electrodes.
– As a result of the global energy transition we are in, durability requirements are becoming increasingly demanding, and justifiably so. We, in turn, make sure that our machinery and expertise match and exceed the requirements placed on them. This allows us to keep offering our global automotive and power transmission customers the most sophisticated capacitor films on the market, Peter concludes.